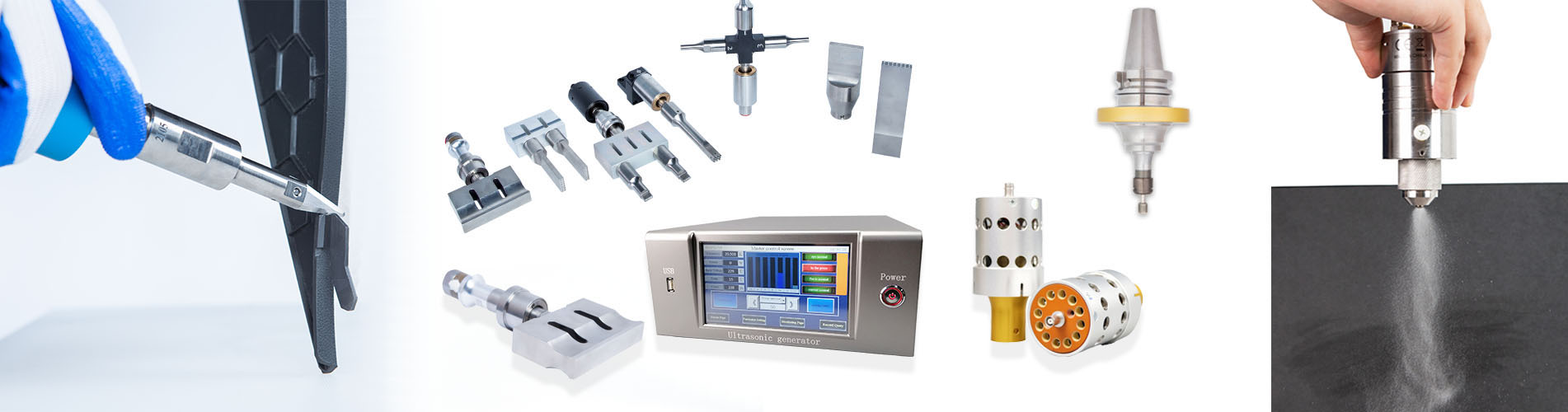
Sonotrode La conception est la clé du succès du soudage par ultrasons des assemblages automobiles
Les zones pourraient rester froids et ne seront pas liés de manière homogène. Avec soudure de vibration, un plastique supplémentaire est nécessaire dans la zone jointe En conséquence, une grande quantité de matière fondu est produite pendant soudage. Ceci matériel pourrait être poussé hors de l'articulation, créant une ligne d'obligation disgracieuse
avantages
Le soudage par ultrasons est également soumis à de telles limitations physiques quand Entrée complexe en forme de 3D pièces. Cependant, si le Sonotrode est correctement dimensionné grâce à l'utilisation de l'analyse des éléments finis (FEA), de soudage ultrasonique offre de nombreux Avantages:
·Les géométries asymétriques inégales peuvent être soudées.
·Les surfaces de composants délicats restent sans marque.
·Cycles de soudure courts entre 100 et 300 millisecondes.
· ciblé rgy L'entrée protège les éléments électroniques sensibles éléments.
·Différents types de matériaux peuvent être soudés ou liés par Incorporation.
·Empreinte de la machine plus petite Com paré à une autre jointure Processus.
· À Donner aux ingénieurs une idée de l'importance de Sonotrode Conception de la soudure réussie, cet article examine trois applications récentes impliquant Automotive Assemblages.
Dans une application, Herrmann était chargé de soudage revêtement en aluminium panneaux d'isolation pour le moteur compartiment. La combinaison matérielle était un tueur: Revêtement en aluminium Polyuréthane (PU) Les tapis acoustiques devaient être liés à fibre de verre Polypropylène renforcé (pp) panneaux. Si que n'était pas Assez de défi, six parties différentes devaient être soudées.
Ceci L'application représentait un véritable défi pour une jonction permanente et sûre des composants adhésifs serait ne fonctionne pas en raison de considérations de coûts et de la combinaison de matériaux. Les éléments de serrage ou des vis étaient trop risqués, parce que Ils pourrait devenir lâche pendant Moteur Opération. Aucune des autres méthodes de jonction thermique, telles que le soudage au laser, le soudage infrarouge ou le soudage des vibrations, ont été appropriés.
Tests initiaux utilisant un soudeur ultrasonique de poche prouvé positif. un joint serré pourrait être créé entre le tapis PU et la injection moulée par injection PP partie, malgré l'aluminium intermédiaire couche. Il était possible pour les vibrations ultrasonores de pénétrer dans le revêtement d'aluminium et d'alimenter les molécules dans le PP partie.
La tâche est ensuite devenue comment obtenir des résultats de soudure répétables et assurer le force de résistance à la traction d'au moins 50 newtons par soudure spot. Résistant à l'usure L'acier durci s'est avéré être le bon matériau pour le Sonotrodes. HERRMANN Les ingénieurs ont déterminé les emplacements de points de soudure et ont conçu les appareils complexes, y compris le système de serrage et la numérisation de pièces Capteurs.
Le Sonotrodes ont été montés sur des actionneurs pneumatiques attachés à six axes robots. Six appareils différents ont été conçus pour correspondre aux formes de la pièce et pour soutenir la soudure SPOTS.
L'assemblage a lieu sur l'indexation rotative Tables. En deux positions, l'assemblage est effectué par deux robots. À une troisième position, un autre robot charge automatiquement et décharge automatiquement les pièces Pièces.
précieux temps supérieur à une seconde par Soudure Spot-a été sauvé par Préchargement le cylindre pneumatique qui s'étend et rétracte l'ultrasons pile. Préchargement signifie que le cylindre a déjà été étendu via Un système pneumatique intelligent avant que le robot apporte l'outil de soudure en contact avec la soudure Spot.
Une autre application impliquait l'assemblage de la journée en cours d'exécution Lumières. Une lentille en plastique transparente devait être soudée à un corps en plastique avec un joint hermétique La surface de la classe 3D complexe et la classe A était un défi pour Soudure. Le client avait également besoin d'un système rentable qui pourrait Accueillir de nombreuses variantes pour diverses voitures Modèles.
À Résolvez le problème, nous avons développé un composite Sonotrode séparé en deux éléments: a bloc-block Sonotrode et un certain nombre de visages individuels conseils. Chaque pointe est une hauteur différente pour s'adapter à sa lentille Exactement.
À garantir la vibration correcte, le transporteur Sonotrode a été conçu avec l'aide de FEA et ajusté pour la fréquence correcte, la puissance de ralenti et amplitude. De plus, chaque extrémité a été conçue, fabriquée et réglée comme une Sonotrode autonome. Les conseils comprennent des fonctionnalités pour divers contours interférents. Pour Par exemple, certains conseils ont des découpes pour accueillir des lettres surélevées sur un composant. Toutes ces influences Comment le Sonotrode vibre.
À Assurez-vous que les conseils vibrent correctement, ils ont été testés individuellement et ajustés dans une prise de paines et manuel de consommation de temps Processus. Sous la simulation de charge, le composite complété Sonotrode a été mesuré au laser et toutes corrections ont été effectuées par CNC usinage. Mesures logicielles spéciales jusqu'à 100 points pour créer l'amplitude Profil. Une fois calibré, le composite Sonotrodes travaillé magnifiquement et ont été vendus à plusieurs reprises.
À Assembler des variantes de modèle, toutes les parties du système ultrasonique forment un "Quick-Change Outillage Cadre " qui peut être détaché de la machine principale et échangé avec un cadre différent Pendant La phase de démarrage, montage a été réalisée avec une machine et plusieurs outillages Cadres. Comme les variantes ont augmenté, le client n'a besoin que d'acheter des outillages supplémentaires Cadres. Coût coûteux Les composants, tels que les générateurs à ultrasons, les commandes et les systèmes de sécurité, peuvent être utilisés avec plusieurs cadres d'outils pour diverses lumières de jour.
Une autre application impliquait une liaison équilibrage de la pression membranes à pomper boîtiers. Les boîtiers sont fabriqués de Fiber-Fibre-renforcé polyphénylène sulfure (PPS). Les membranes sont en polyester ou polycarbonate. Le client voulait remplacer cher Precut membranes simples avec membrane moins coûteuse ruban adhésif.
Ceci était une application exigeante, parce que Trois étapes de processus ultrasonique consécutives devaient être Réalisation:
·frapper la membrane et le souder à une casquette (35 Kilohertz).
·fournir au capuchon avec une couverture de protection (35 Kilohertz).
·soudage du capuchon complet au boîtier (20 Kilohertz).
Notre Un système d'outils ultrasonores nouvellement développé, MPW, ne fait que ça. Il pointe et joint en même temps à l'aide d'une bande membranaire sur un rouleau, économisant de l'argent
© droits dauteur: 2025 Hangzhou Altrasonic Technology Co.,Ltd Tous les droits sont réservés
IPv6 réseau pris en charge
Scanner vers wechat